Noticias
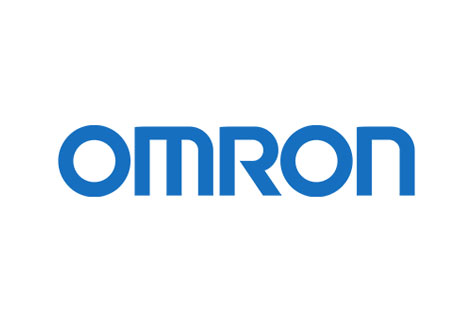
El alcance de la trazabilidad ha crecido con los avances en tecnología digital, haciendo de esta una aplicación crítica y ubicua para los fabricantes de clase mundial.
En nuestros días, la trazabilidad es un término comúnmente empleado en la manufactura y en la gestión de la cadena de suministros.
Tal como sucede con muchas frases que hoy escuchamos en la industria (como el Internet Industrial de las Cosas), la trazabilidad puede significar cosas diferentes para la gente o las organizaciones.
Es debido a esto que el término “Trazabilidad 4.0” ahora describe las fases actuales y futuras de la trazabilidad en su contexto global. Las definiciones de trazabilidad han evolucionado desde la invención de los equipos de captura automática de datos (principalmente los lectores de código de barras) en los últimos 40 años. Desde entonces, las aplicaciones se han transformado para apoyar el desarrollo industrial tanto por el lado de la tecnología del producto como desde la perspectiva del proceso de negocio.
La trazabilidad 1.0 consiste en identificar productos de manera automática para alcanzar la productividad y la eficiencia.
Los lectores de código de barras, que fueron utilizados en un principio en procesos de manufactura sencillos, han tenido una adopción vertiginosa. La habilidad de marcar una parte y luego darle seguimiento fue sin duda un parteaguas.
Esta tecnología se convirtió, y sigue siendo, en un elemento indispensable en la manufactura para mejorar la eficiencia y productividad de las operaciones. A menudo, de hecho, es el primer paso para la implementación de soluciones de trazabilidad.
Su primera gran escalada comercial se presentó en las operaciones de retail. Antes, los cajeros tenían que teclear el producto y el precio en una caja registradora. La captura automática de datos de los sistemas de código de barras generan un enorme ahorro de tiempo, mejoran la precisión e incrementan rendimiento. El primer Producto Universal de Código (UPC), lanzado en 1974, aún está en uso.
Otra adaptación del uso de código de barras, que sigue siendo predominante, es el de los tubos de ensaye de 1D empleados para especímenes humanos y animales. Los tubos de sangre o de material biológico se envían a laboratorios donde son colocados en instrumentos de diagnóstico clínico. Estos instrumentos corren varias pruebas o muestras, tales como paneles de lípidos y otras pruebas médicas. El código de barras se utiliza para hacer un seguimiento individual de especímenes y así asegurar que los resultados sean asociados con el paciente indicado. En la actualidad existen muchas más aplicaciones en uso. La Trazabilidad 1.0 es transformacional en la manufactura y en la industria debido a la eficiencia y a la precisión lograda al procesar un elevado número de artículos o transacciones de manera discrecional.
La cadena de suministros
El código de barras se aplica a artículos fabricados y los manufactureros identifican nuevos usos. Pueden dar seguimiento a los materiales dentro de la planta y a lo largo de toda la cadena de suministro.
Ahora es posible hacer un seguimiento exhaustivo desde la materia prima hasta el producto terminado con el propósito de optimizar la gestión del inventario y reducir los costos. Al mismo tiempo, los consumidores se vuelven más conscientes en términos de calidad y salud, además de que los medios se vuelven más agresivos para la cobertura de problemas de calidad en los productos.
La trazabilidad 2.0 se refiere a la administración de los inventarios y a satisfacer las necesidades de la sociedad.
Nadie quiere verse en un tema relacionado con la devolución de la compostura de un producto nuevo, ni el fabricante, ni el proveedor ni el cliente. Los defectos en los productos y las devoluciones pueden ocurrir en cualquier industria. Algunos tal vez aún recuerdan el problema de Tylenol en 1982, un incidente que propició una reforma en el empaque en la industria farmacéutica.
El costo entonces se calculó en 100mdd. En 2000, Bridgestone y Ford perdieron reputación de manera masiva y gastaron alrededor de 5.6 mmd a causa de defecto en llantas. Se tuvieron que devolver aproximadamente 20 millones de neumáticos. En 2016, el retiro del teléfono Not T de Samsung Note debido a peligro por quemaduras aún causa indignación. En la actualidad, a lo largo de todas las industrias y sus cadenas de proveeduría, las devoluciones pueden causar serios problemas. La demanda de trazabilidad 2.0 se ha disparado para abordar estas necesidades.
Con esto se pueden aislar los productos con defectos según sus códigos de fecha y de lote, con lo que se reduce el costo de calidad y se incrementa la confianza del consumidor, al tiempo que los fabricantes pueden identificar la fuente del problema en sus procesos. Se ha informado mucho sobre productos defectuosos en muchas industrias, desde alimentos contaminados hasta piezas de automóviles defectuosas.
En los puntos de venta se ha presionado a los fabricantes para que incorporen componentes de trazabilidad y solicitan códigos de barra para elevar sus estándares de calidad. Esta industria, así como la FDA (la Administración de Fármacos y Alimentos estadounidense) para fabricación de dispositivos médicos UDI (Identificador Único de Dispositivos), han adoptado las especificaciones de calidad ISO de código de barras, lo que impacta en muchos niveles de las cadena de suministro.
Líneas de artículo
La trazabilidad 3.0 se refiere a la optimización de la seguridad en la manufactura y la cadena de suministros al enfocarse concretamente en los materiales, la segunda de las 4 Ms de la Manufactura Esbelta (Man, Material, Machine, Method).
En este caso, el material aplica a todo lo necesario apra construir un producto determinado: materia prima, componentes y subcomponentes, así como el producto terminado con número de serie.
Los fabricantes comenzaron a extender la trazabilidad a sus proveedores al solicitarles la colocación de códigos de barra y otros datos de identificación en los componentes y empaques.
Algunos se refieren a estos como trazabilidad de componentes, subcomponentes y artículos de línea.
Mientras más proveedores agregan información, los proveedores son más capaces de optimizar los procesos de fabricación y la calidad de los productos, incluso más al emplear la trazabilidad en la planta de manufactura.
La trazabilidad 3.0 también implica la habilidad de desempeñar acciones de control preventivo ante una emergencia o un evento relacionado con la calidad.
Los subcomponentes pueden ser identificados, monitoreados e inspeccionados por el área de calidad antes del ensambile final.
Cuando un fabricante es capaz de volver hasta el último punto de revisión aceptable, los ajustes se pueden hacer en la producción final para asegurar las calidad de los productos antes de ser embarcados.
La introducción de sistemas como Data Matrix (desarrollado por una de las empresas adquiridas por la firma Omron) y otras simbologías 2D facilitan enormemente la trazabilidad 3.0, pues los símbolos son mucho más pequeños que su contraparte 1D y pueden contener más datos. Esto es especialmente importante en la industria electrónica, donde los componentes de los dispositivos reducen permanentemente sus dimensiones.
El desarrollo de la Marca de Pieza Directa (DPM) se presenta en esta fase de la evolución de la trazabilidad debido a la necesidad de identificadores más robustos para resistir la fabricación o los entornos duros. Los fabricantes graban los símbolos DPM directamente en materiales como metal o plástico y eliminan el empleo etiquetas frágiles.
Finalmente, la trazabilidad 3.0 permite que los fabricantes tengan una habilidad mayor para asegurar la autenticidad de los productos y enfrenten mejor problemas de falsificación.
Solo en la industria automotriz, la falsificación de partes se estima entre 10 y 30 mmd cada año. Al identificar todos los componentes en un ensamble o producto y al mejorar la resistencia de los códigos de barra de 1D y los símbolos 2D, se ha podido avanzar mucho en la lucha contra la falsificación en toda la cadena de suministros.
Viabilidad del proceso
Hasta ahora, hemos hablado de producto, componente y seguimiento de la cadena de suministro como objetivos clave del monitoreo.
La trazabilidad 4.0 es la unión de todos estos elementos, junto con los parámetros de la máquina y el proceso para lograr el más alto nivel de fabricación.
Esto incluye la eficacia general del equipo (OEE), así como los datos de producción y calidad para mejorar la efectividad general de la fabricación.
Aunque algunos fabricantes ya emplean tecnología de trazabilidad 4.0, esta representa el futuro para la mayoría de las empresas.
Una buena analogía para representarla es con la implementación de la trazabilidad en el contexto de las 4 Ms de la Manufactura Esbelta. Los fabricantes ahora pueden conocer todo lo que ocurre en su empresa en relación con una parte o un producto, incluyendo su genealogía completa.
La trazabilidad 4.0 mejora mucho los análisis de causa raíz.
¿En qué máquina se fabricó una pieza y en qué momento? ¿quién estaba operando la máquina? ¿Dónde se localizaron los cuellos de botella? Ños escenarios de diagnóstico potenciales prácticamente no tienen límite.
Por ejemplo: la temperatura y torque de una máquina estaban dentro de especificaciones y sin embargo operaron sobre los límites de control cuando ocurrió una falla. Al tener esta información, potencialmente podría permitir al fabricante ajustar los límites máximos de control de la máquina y permitir que se mejore el proceso.
Las mejoras sustanciales se presentan en muchas áreas con la Trazabilidad 4.0. La habilidad de identificar fallas específicas de producto con parámetros y condiciones de operación detallados permite tener una análisis de causa raíz más precisa y de manera más oportuna. Los fabricantes pueden también tomar mejores decisiones de producción y procesos.
¿A través de qué proceso se mueve una pieza en particular? ¿Cuáles componentes son empleaos en un subensamble específico? La verificación del ensamble, el aseguramiento de la calidad y el control de las listas de materiales son mejor optimizadas.
En la industria automotriz, la trazabilidad 4.0 puede ir más allá de las dimensiones geométricas y la tolerancias (GD&T). Los componentes que deben embonar con precisión, como el caso de los pistones y los monoblocks, son categorizados e identificados con base en medidas exactas y automáticamente comparados basados en sus números de identificación correspondiente para asegurar una precisión y desempeño máximos.
Un fabricante de la industria electrónica ha desarrollado una solución de Trazabilidad 4.0 con tecnología de la firma Omron para dar seguimiento a un producto a lo largo de todos los pasos del proceso. Cada máquina de perocesamiento escribe un DPM propietario en cada producto para crear una genealogía de manufactura en tiempo real, además del maquinado del producto.
Finalmente, en un estado avanzado, un sistema de trazabilidad 4.0 puede tomar decisiones en automático para optimizar los equipos y procesos basado en datos adquiridos, incluyendo mantenimiento predictivo de manera automática. Esto es facilitado por sensores inteligentes, controladores con inteligencia artificial, sistemas de radiofrecuencia (RFID) y software avanzado de gestión de datos. Este conocimiento del proceso puede llevar a mejoras en otras plantas a lo largo de la empresa y de manera global.
Todos los niveles de trazabilidad son fundamentales para el éxito de una empresa de manufactura. De hecho, la mayoría de las industrias verán y utilizarán todos los niveles en sus plantas o instalaciones. Una fase no es "mejor" que la otra; el complemento completo es su fuerza. La evolución de la trazabilidad es el resultado directo de las necesidades comerciales y es crucial en el mundo hipercompetitivo de la fabricación global.
Andy Zosel es President and Chief Executive Officer, OMRON Microscan.
Con más de 25 años de experiencia en el mercado de tecnología y automatización, su liderazgo y conocimiento incluyen toma de decisiones estratégica, gestión de proyectos tecnológicos y resolución de problemas relacionados con temas de innovación en áreas como ingeniería opto mecánica, desarrollo de procesos, administración de productos y mercadotecnia B2B para tecnología. Con un MBA en la Universidad de Phoenix y una carrera de Ingeniería Mecánica en la Universidad de Washington, ha conseguido 5 patentes, incluyendo 3 relacionadas con Sistemas Micro-Opto-Electro-Mecánicos (MOEMS).
Kenta Yamakawa es Senior Vice President, OMRON Microscan
En los últimos 20 años ha trabajado en tecnología, ingeniería y planeación de mercados. Su especialización se centra en automatización de sistemas sociales y automatización de plantas. Tiene especial enfoque en integración post fusión y estrategias de negocio, así como la supervisión de la ejecución de dichos planes. Como ingeniero en diseño mecánico, ha logrado varias posiciones de liderazgo en plantas de automatización y en la investigación de tecnologías de sensores. Tiene carrera y maestría en Ingeniería Mecánica en la Universidad Metropolitana de Tokio y ha logrado 11 patentes, principalmente relacionadas con el diseño de sensores para automatización de fábricas.
Otros artículos de interés
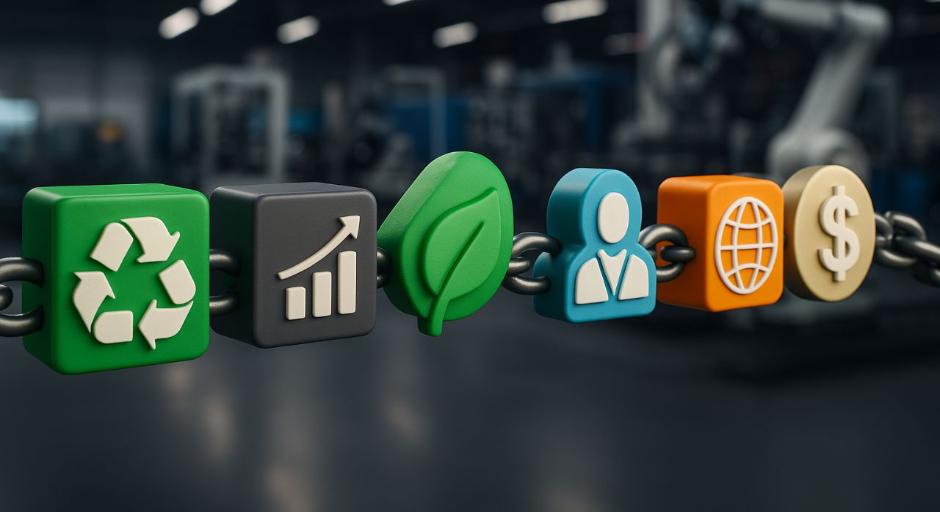
Cuidado ambiental: responsabilidad eslabonada
El cumplimiento de políticas de sostenibilidad en la industria manufacturera se ha
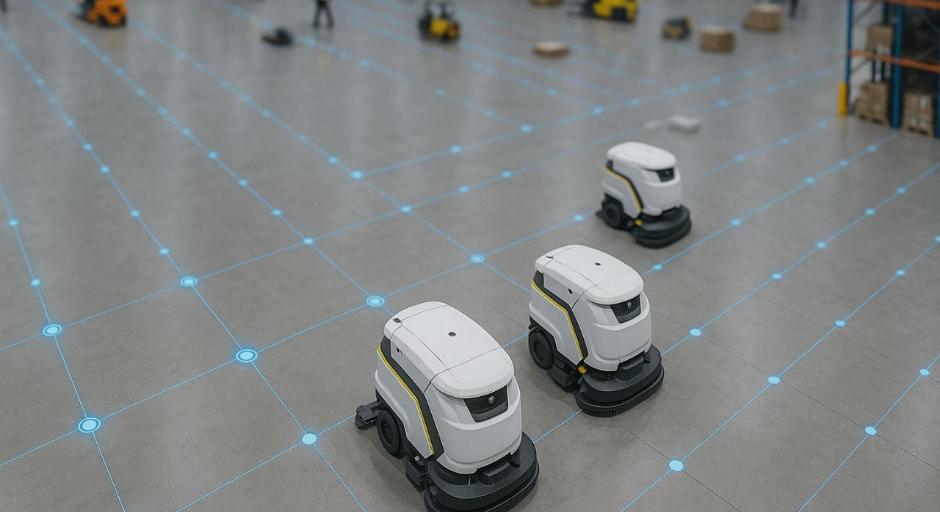
Limpieza industrial no escapa de la automatización
En la industria, la limpieza de áreas productivas es tan importante como
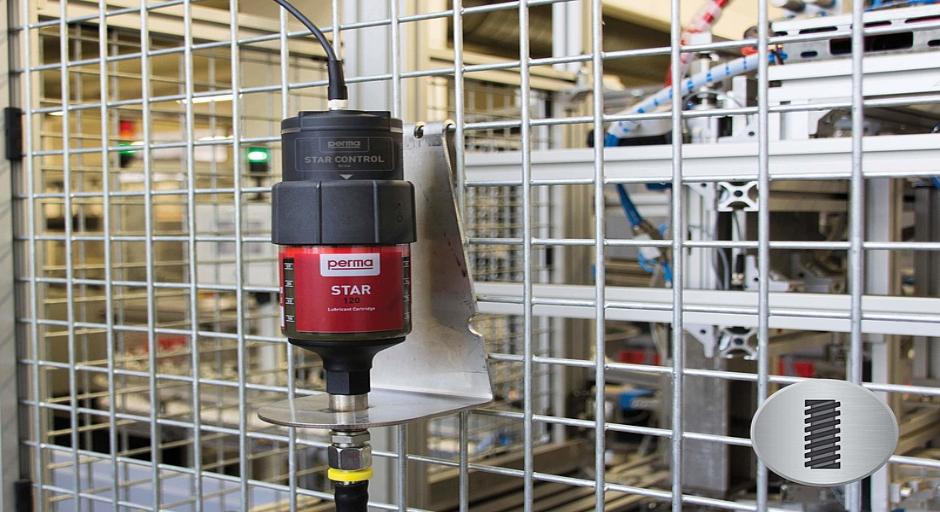
Lubricación automatizada, paso obligado en operación: Perma
En las plantas industriales, la lubricación ha pasado de ser una rutina

Suministro ininterrumpido para la Industria 4.0
La Industria 4.0 representa un salto evolutivo en la manufactura: sistemas físicos,
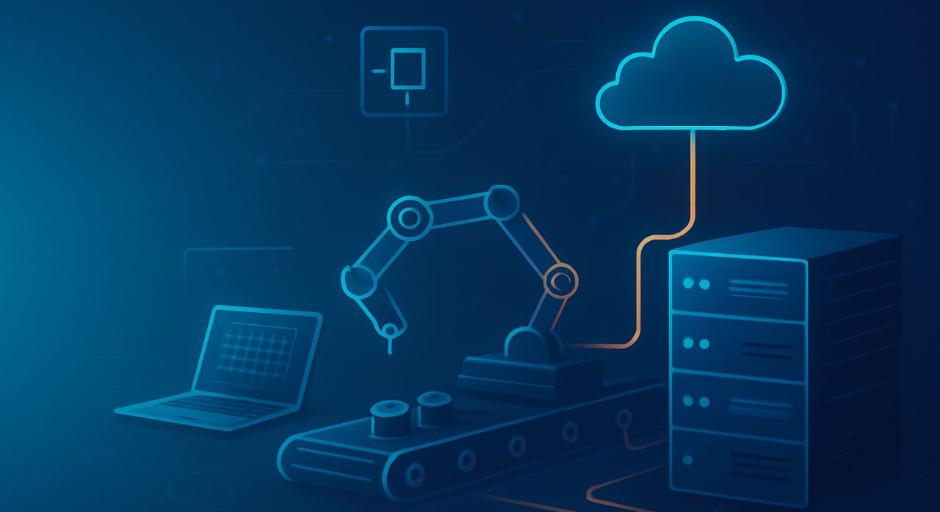
Por qué la manufactura requiere una buena infraestructura de redes
Con la adopción de tecnologías digitales en la manufactura, la infraestructura de

Transporte multimodal gana valor en la industria
En la industria manufacturera mexicana, la logística ha dejado de ser un